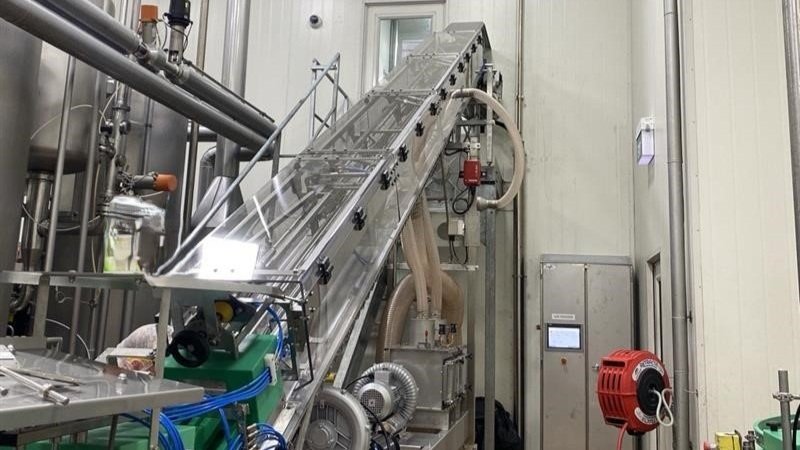
Production Line- Air Rinser
Project Summary for Recent Projects: K211 Air Rinser Replacement
Overview
In a continued effort to enhance sustainability, TPG Projects recently managed the "K211 Air Rinser Replacement" project at a manufacturing facility. This project aimed to reduce water usage by replacing an outdated water rinser with an ionised air rinser in the K211 can production line, which processes cans in 330ml, 440ml, and 500ml formats at high speeds.
Project Scope
The upgrade involved installing an HF Meyer HYION 5000 ionised air rinser, designed to eliminate the need for water rinsing and reduce operational downtime caused by equipment jamming. The new system enhances production quality by leaving no moist residue on cans and supports the facility's dry floor policy.
Key Benefits
-
Sustainability
A significant reduction in water consumption by 2,592 m³ per year, supporting long-term environmental goals.
-
Quality & Efficiency
Air rinsing improves hygiene by leaving cans dry, reduces unplanned downtime, and improves operational efficiency.
-
Cost Savings
Estimated annual savings of $18,745 due to decreased water costs and maintenance requirements.
Outcome:
As part of its sustainability goals, TPG managed the successful replacement of a water-based rinser with an ionised air rinser on the K211 production line at a leading beverage manufacturing facility. The project involved installing the HF Meyer HYION 5000 system to improve efficiency, eliminate water use, and support dry floor operations.
The new air rinser handles multiple can formats (330ml, 440ml, and 500ml) at high speeds, reducing equipment jamming and removing moisture-related issues. This upgrade delivers cleaner, more reliable rinsing while supporting the client's sustainability and operational performance targets.
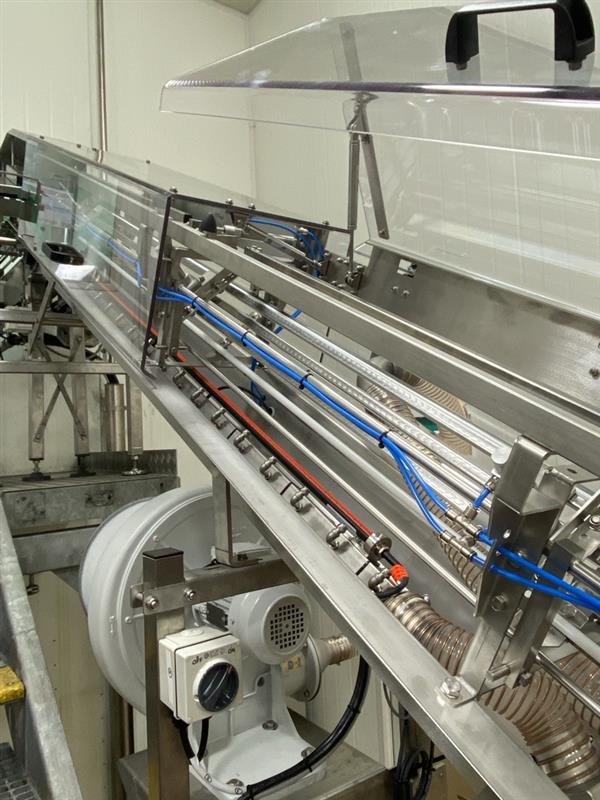
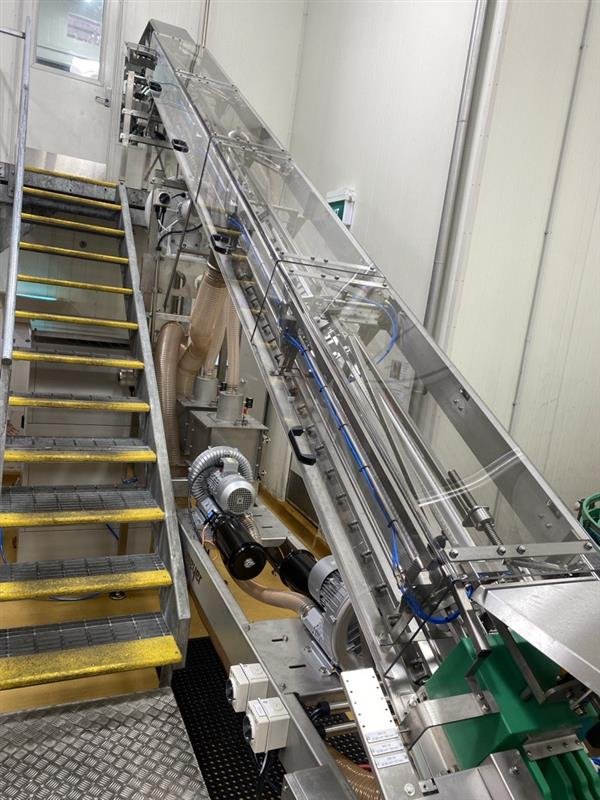
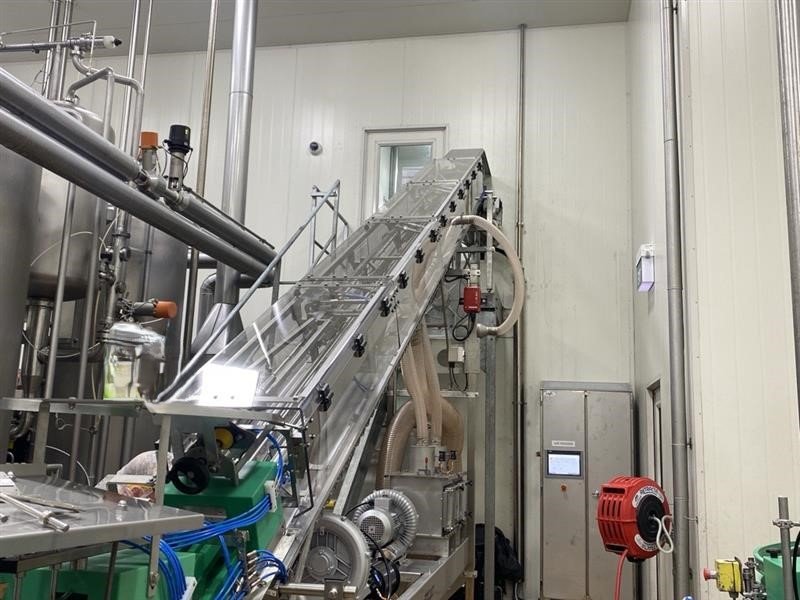