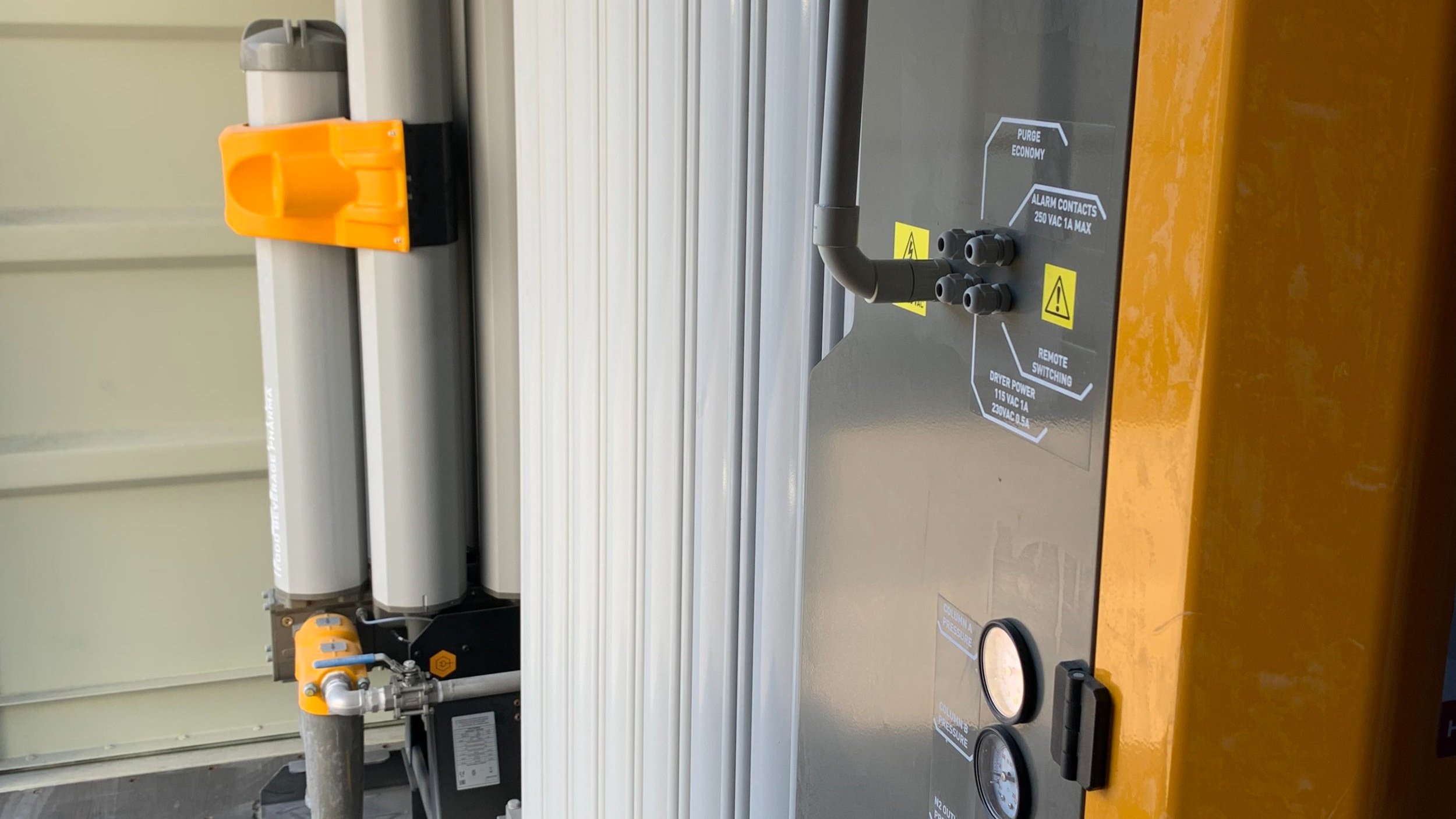
PSA Nitrogen Generator
Overview
TPG Projects recently undertook the installation of a nitrogen (N2) generation unit at a major manufacturing facility in Wiri, New Zealand. The project aimed to replace carbon dioxide (CO2) with nitrogen in the gassing process for can seamers, providing a stable, cost-effective, and sustainable solution for product packaging.
Project Scope
The project included purchasing and installing a stand-alone nitrogen generation plant using Pressure Swing Absorption technology. This technology produces food-grade nitrogen, ensuring a consistent supply for the client and aligning with stringent food safety standards. The system was set up in a custom enclosure with all necessary electrical and piping installations.
Key Benefits
-
Cost Efficiency
Achieved significant savings with nitrogen generation costs at $0.02/kg compared to $1.54/kg for CO2, resulting in annual savings of approximately $77,982 for select product lines.
-
Supply Stability
The switch to on-site nitrogen generation minimizes reliance on external CO2 suppliers, reducing risks related to supply chain disruptions.
-
Quality Assurance
The nitrogen produced meets food and pharmaceutical standards, ensuring compliance with both European and U.S. regulatory guidelines.
Outcome:
TPG successfully managed the installation of a stand-alone nitrogen (N₂) generation plant at a major beverage manufacturing site in Wiri, New Zealand. This $355,000 project replaced CO₂ with nitrogen in the under-cover gassing process for can seamers—delivering a more stable, cost-effective, and sustainable solution for packaging operations.
The system, based on Pressure Swing Adsorption (PSA) technology, produces food-grade nitrogen on-site at a fraction of the cost of CO₂. It was installed in a custom containerized enclosure with full electrical and piping integration, and includes high-purity gas delivery, safety controls, and gas detection across key filling areas.
The project delivers annual savings of nearly $78,000, improves supply security, and aligns with global food safety standards. Despite minor risks around can seam integrity for select products, the transition supports long-term operational resilience and environmental goals.

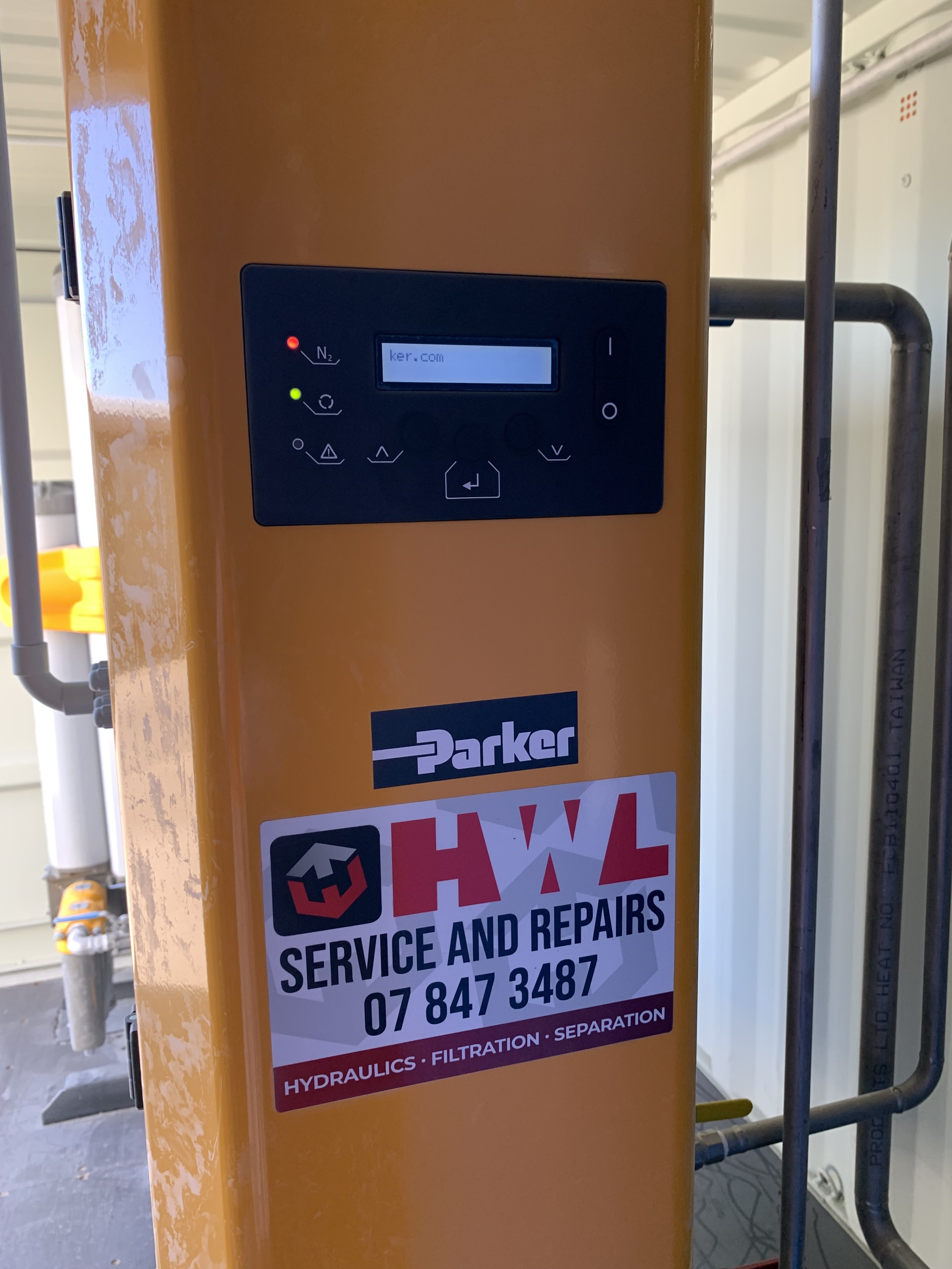
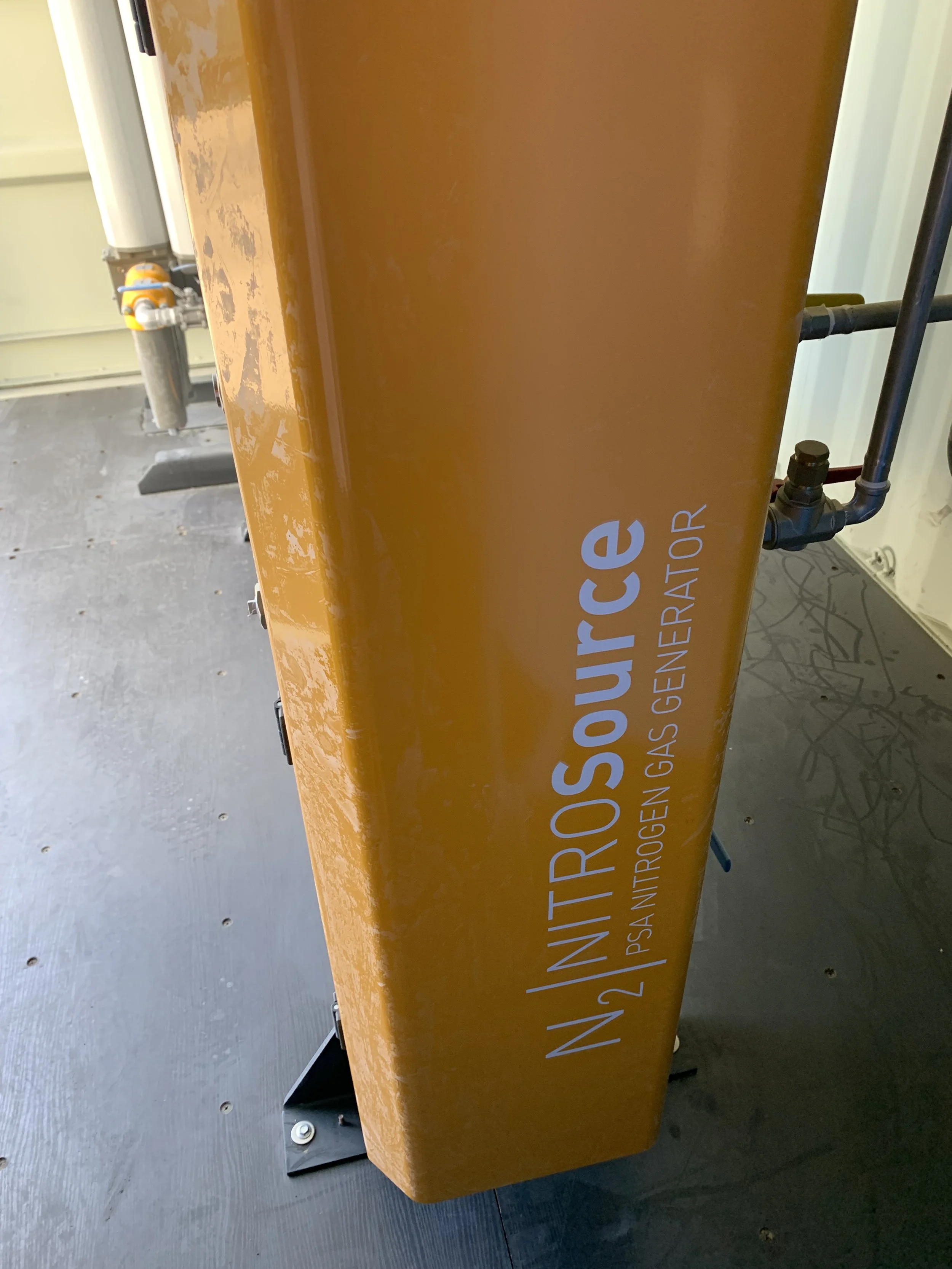
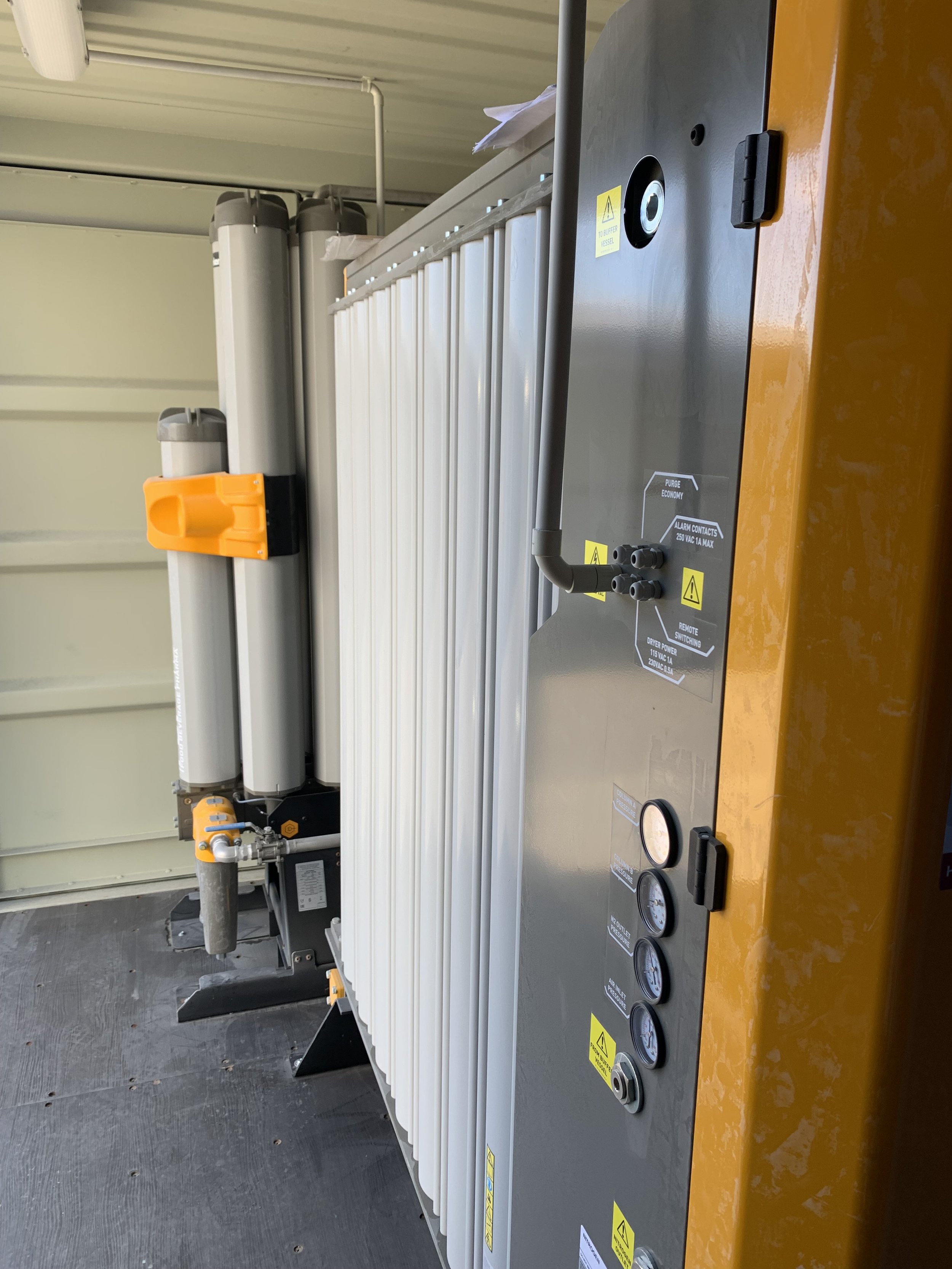
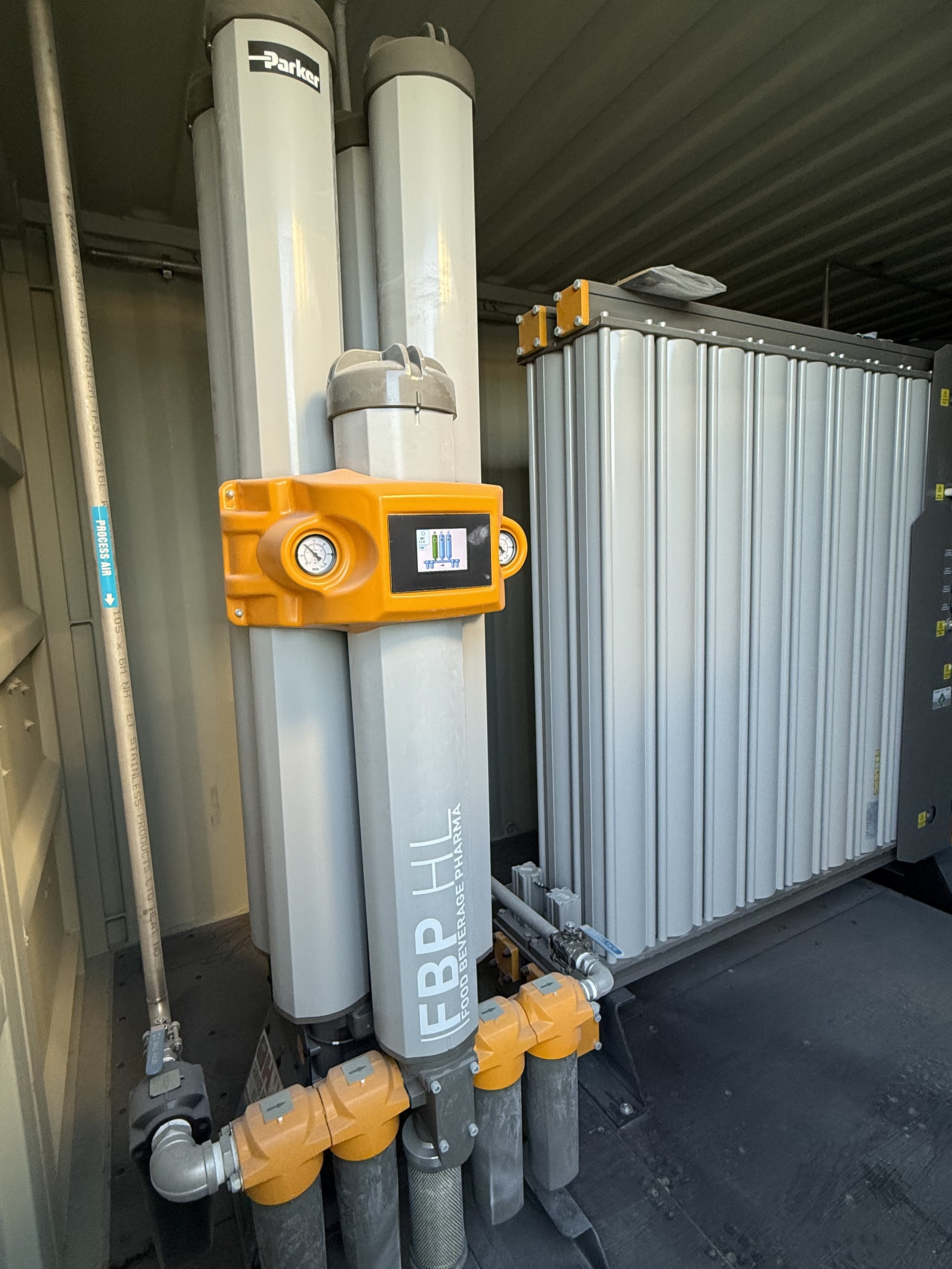
